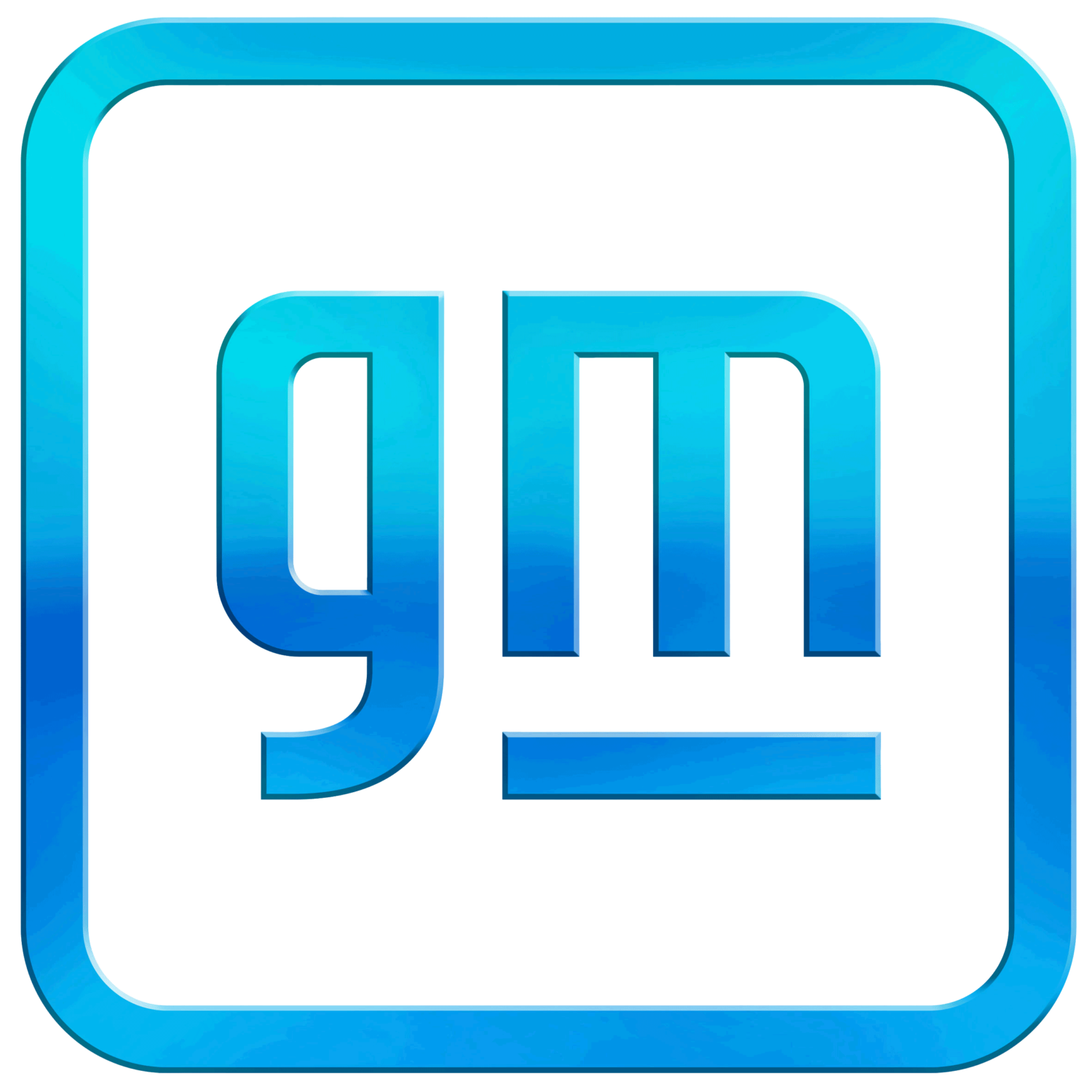
GM Gripper Challenge
GM’s Gripper Challenge, in partnership with MassRobotics
GM Gripper Challenge sought startups, academia and integrators to develop a proof-of-concept universal end effector capable of grasping and holding a variety of sheet metal components for purposes of precise robotic assembly.
Read more about the challenge and winners here: MassRobotics Announces Winner of its GM Gripper Challenge.
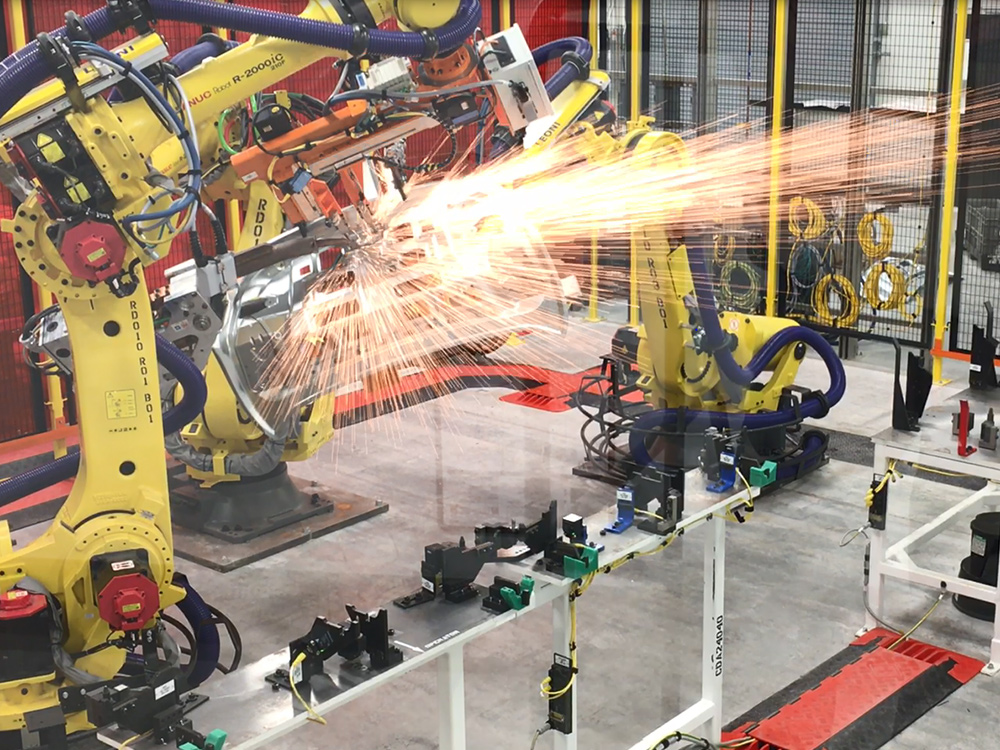
More info
GM partnered with MassRobotics to hold a Gripper Challenge reaching out to startups, academia and integrators to develop a proof-of-concept universal end effector capable of grasping and holding a large variety of sheet metal components for purposes of precise robotic assembly.
The end effector must be capable of holding the parts firmly enough to enable precise part alignment (using sensor-based robotic control) and subsequent processing (e.g. resistance spot welding).
Key performance metrics for concept selection include: geometric flexibility, holding force, cycle time, reliability, and complexity.
The end effector must:
- Hold 12+ different parts
- Hold up to 25lbs
- Be capable of precision alignment with parts
- Use sensor-based robotic control
- Endure spot welding and other processing while gripping
- Minimal integration and self-contained
Performance was judged on:
- Flexibility
- Holding force
- Speed (Cycle time < 5 sec)
- Reliability
- Complexity
Subscribe to the MassRobotics Newsletter
Learn about our residents and partners, participate in our events and challenges, and receive robotics and AI industry news.